A client reached out through our website, searching for a reliable partner to create their jewelry collection – stainless steel pieces covered with silver plating.
Despite outsourcing their products to numerous jewelry makers, they need help finding the right one with the right skill set and expertise. Their previous pendants usually end up going black and oxidizing quickly. Even a slight touch of the fingers leaves scratches on the plated jewelry’s surface, leading to a poor brand image that affects their sales and reputation.
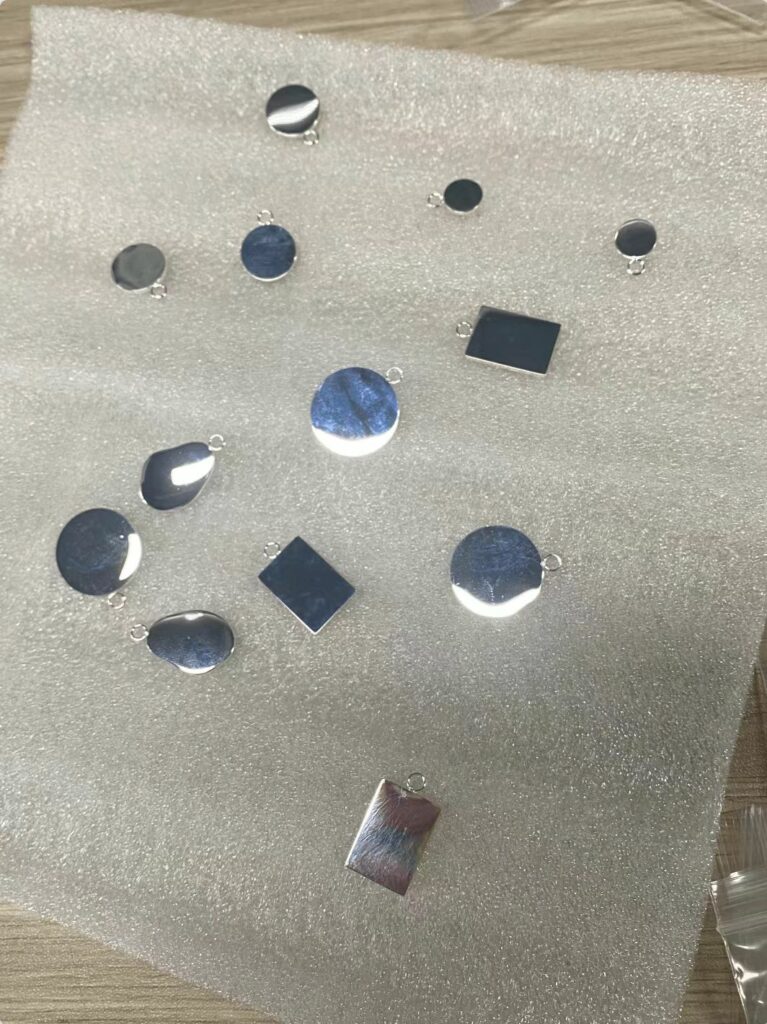
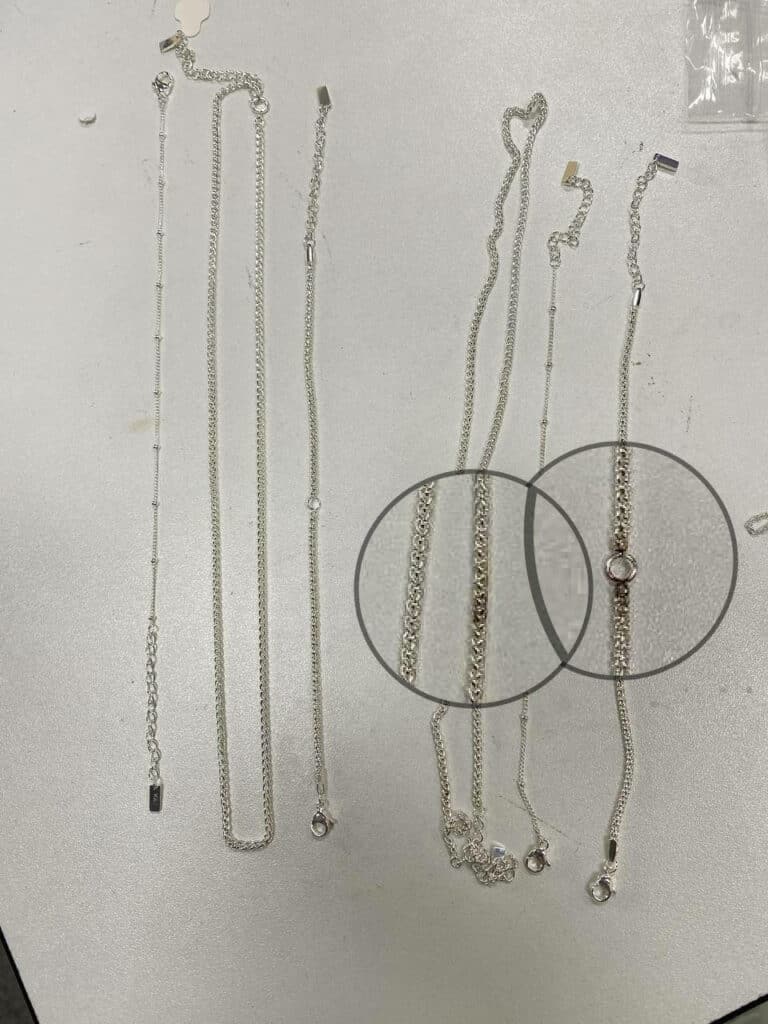
A REAL Challenge Despite of Our Decades of Experience
The client’s jewelry collection has a stainless steel base, so it’s usually plated using Physical Vapor Deposition (PVD). In this process, the material (TiN and Au) is turned into a vapor that is then transported to the jewelry piece through a vacuum or low-pressure gas.
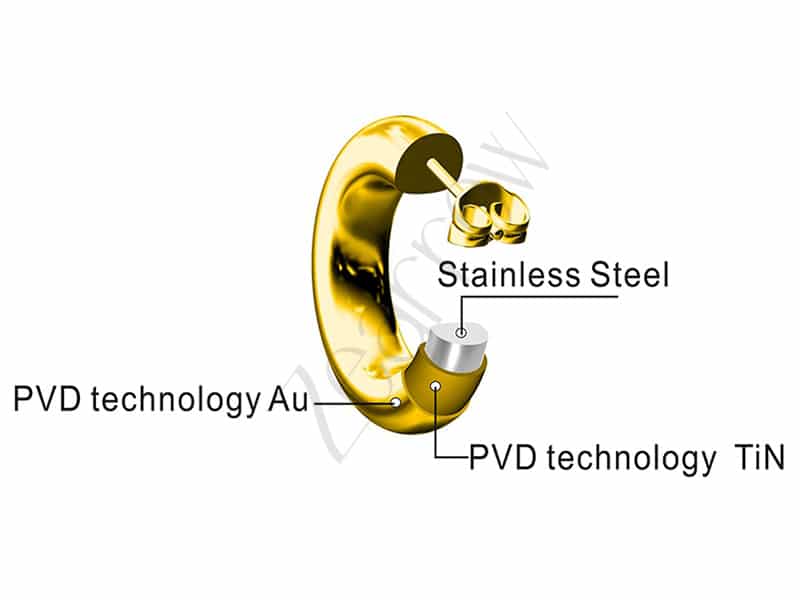
However, PVD cannot be used for silver plating. To meet the client’s requirements, we had to use the electroplating technique, commonly applied on brass or silver. Few factories have attempted this, and it is also the first time for Zearrow to try silver plating on stainless steel.
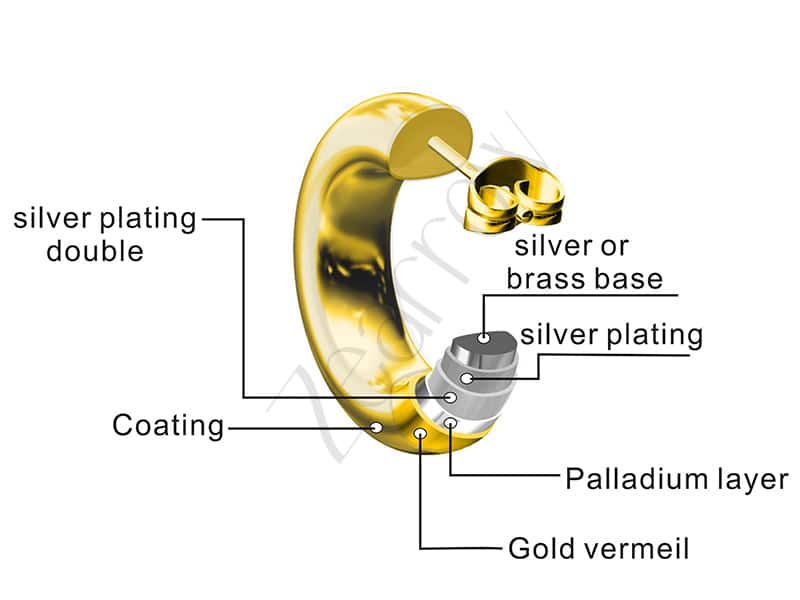
This presents a significant challenge for us: can we achieve the desired silver color? Will the coating maintain durability and corrosion resistance?
Extra Tips: Rhodium Plating vs. Silver Plating
2 common methods professional jewelry makers use to achieve a silver color on steel jewelry are silver plating and rhodium plating.
Some benefits of rhodium plating include the following:
High Durability – as a material, rhodium is harder than silver, thus providing better scratch and wear resistance to the jewelry piece.
Tarnish Resistance—Another great property of rhodium is its better resistance to tarnishing, which allows the jewelry to retain its fresh and distinct look longer.
Hypoallergenic Properties—Rhodium-plated jewelry is inherently hypoallergenic, making it great for even those with sensitive skin.
Despite the advantages of rhodium plating for jewelry, the client still prefers silver plating for its brightness and luster. Respecting this decision, we proceeded to find ways to make high-grade silver-plated jewelry for the project.
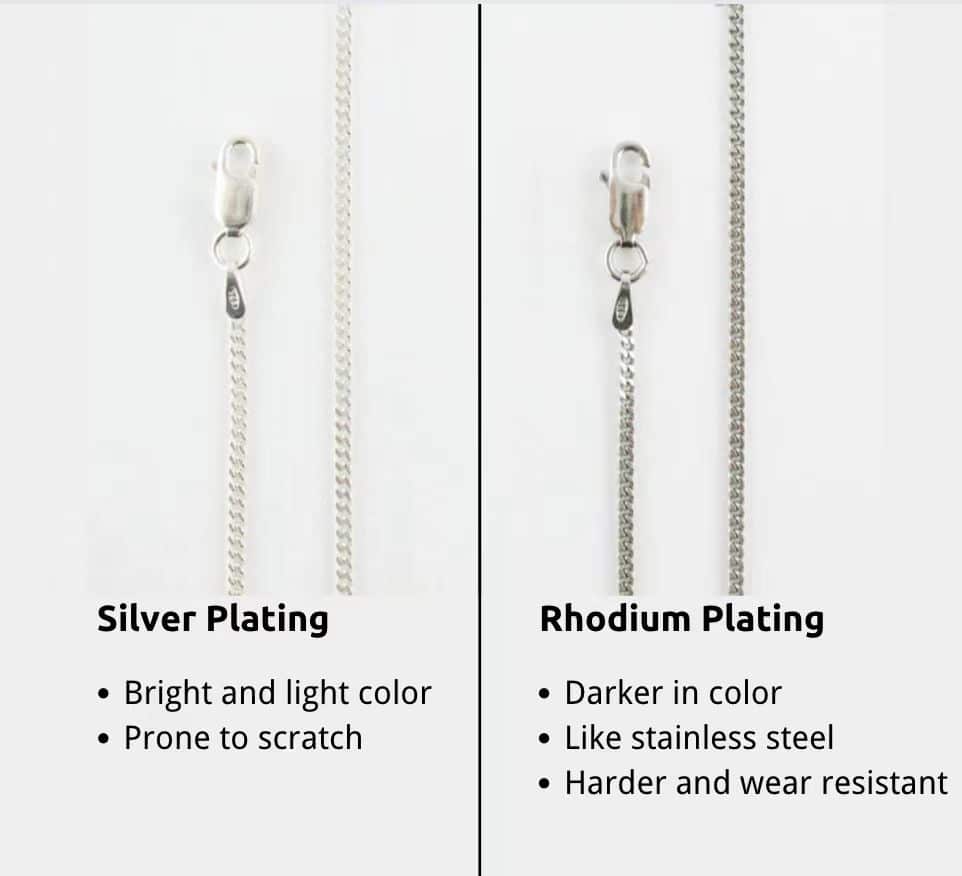
Reasons Why the Pendants Perform Poorly
Before taking on the challenge, we requested a pendant from our client to understand why it oxidized so quickly. Receiving the sample, our team had a test on the plating payer and finally determined what was causing their jewelry pieces’ poor performance. Some key points we’ve noticed were:
Absence of Electrophoretic Coating
We’ve deduced that the rapid oxidation of their silver-plated jewelry is due to the pieces’ lack of an electrophoretic coating. The electrophoretic coating protects the silver from air exposure, reducing the risk of oxidation and blackening.
Insufficient Plating Thickness
As for the quick scratching of the plated surface, we figured out that the silver plating covering the pieces was too thin to protect the base. Whether due to budget constraints or tight deadlines, thin silver plating won’t provide the proper protection or durability the jewelry pieces need.
Lack of Production Experience
While the last jewelry manufacturer they worked with knows their way around stainless-steel products, they don’t have enough experience in silver plating. They will likely outsource their electroplating to another company, resulting in poor quality control.
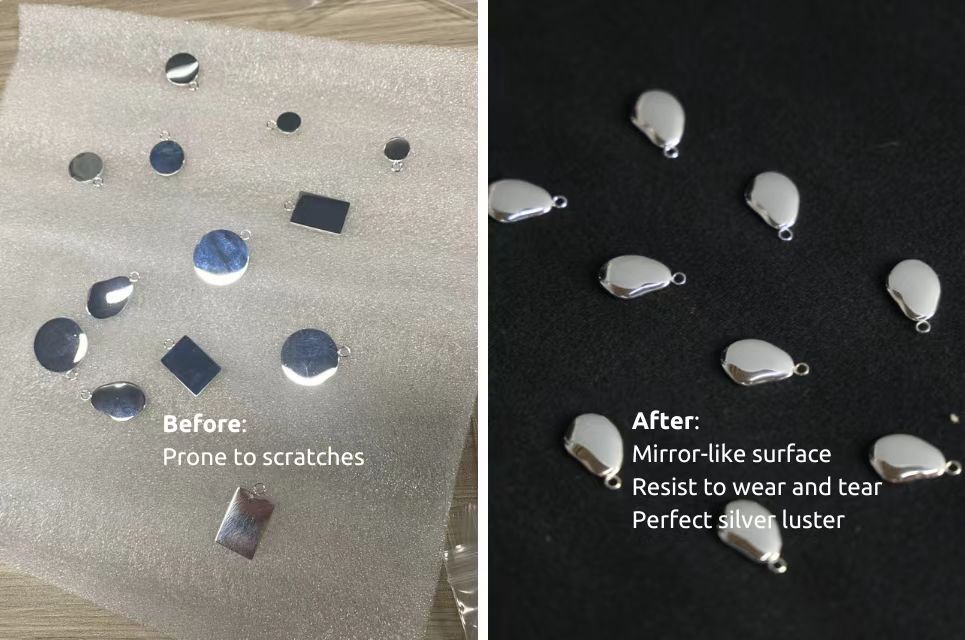
Electroplating as An Savior
A significant factor in this project’s success is how we approach the plating process. While PVD offers various benefits, it doesn’t work for silver plating.
After discussions, we decided to use electroplating to coat the pieces with top-grade silver. This method not only enhances the jewelry’s resistance to rust and corrosion but also results in a beautiful finish that customers will love. Additionally, we can calibrate the silver plating to be thick enough to resist scratches and daily wear, extending its lifespan while maintaining an excellent appearance.
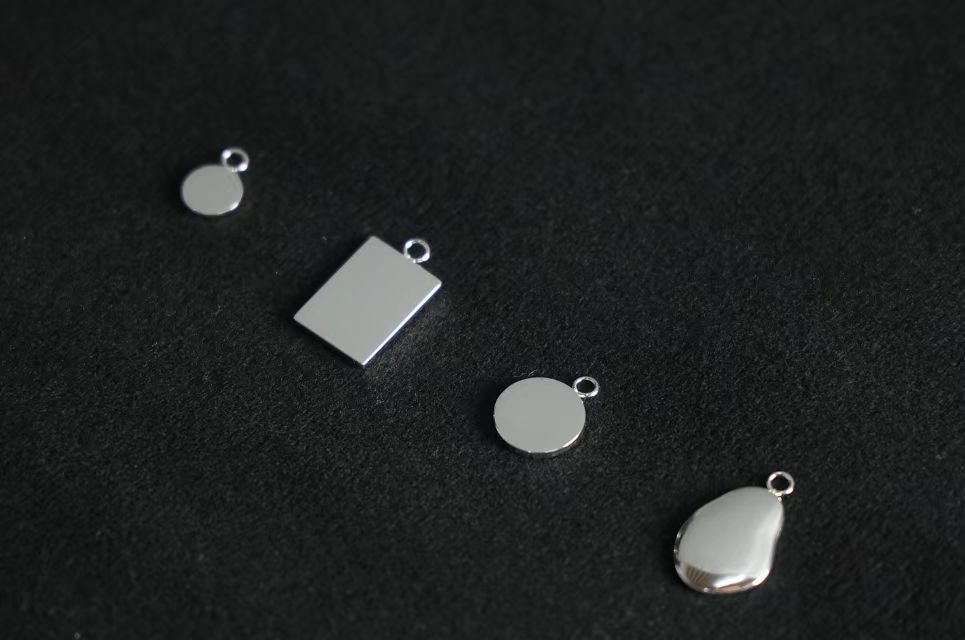
How Zearrow Does It Better
After finalizing all the information we needed, our team conducted extensive research to develop the perfect technical solution for the obstacles presented. We then tackled the project with foolproof direction, which included:
Improving Plate Thickness
To address the issue of the surface easily scratching and damaging, we decided to coat the piece with a thicker silver plating. This better protects the jewelry piece, leading to better scratch and wear resistance.
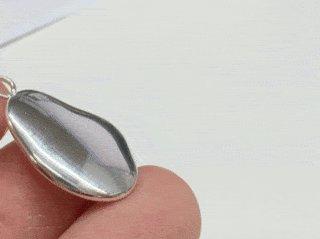
Electrophoretic Plating
In addition to a thicker silver plate, we also upgraded the coating process to electrophoretic plating. Although similar to electroplating, e-coating is another plating technique that covers the jewelry piece with a layer of metal. Also referred to as electrocoating, this makes the jewelry piece more resistant to air and humidity—the leading cause of oxidation in silver-plated jewelry.
Meticulous Quality Control
From meticulous sample-making to rigorous testing, we practice the highest standards in jewelry production to produce pieces worthy of any brand. Our commitment to quality makes Zearrow stand out from your run-of-the-mill manufacturer, promising the elevation of your brand recognition and sales.
Prompt Communication
During our trial process, we anticipated slight delays that were immediately communicated to the client. While they were pleased with the initial results of our testing, we continued to improve and refine the process for better output. This ultimately led to a final product that exceeded and satisfied their expectations.
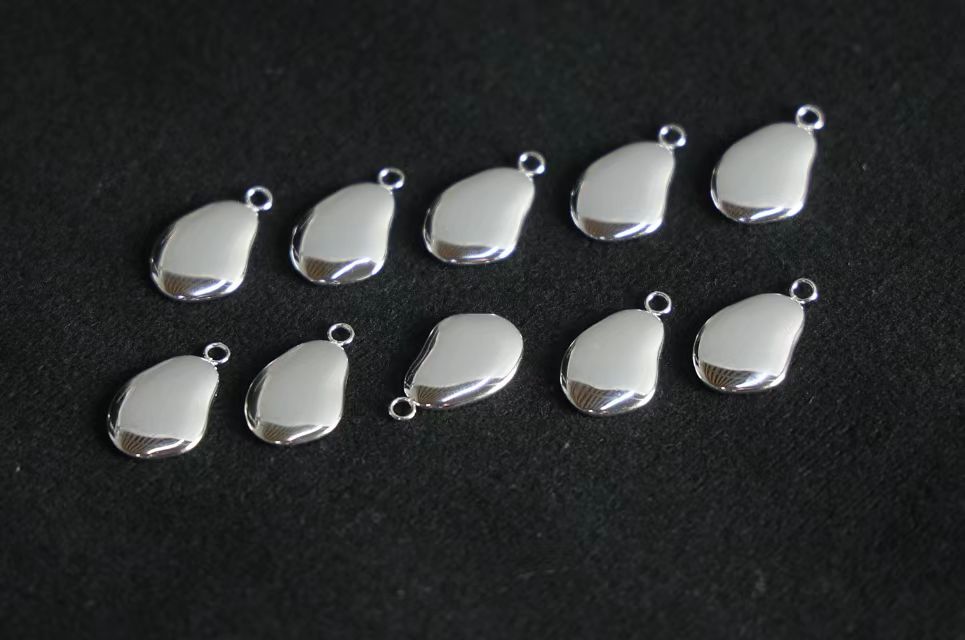
We’re Not Just Manufacturers – We’re Your Dependable Business Partners
In the end, we leveraged our robust experience and skill in electroplating and quality control to produce fine jewelry pieces that won’t easily tarnish, scratch, or oxidize. The client was fully satisfied with the results and will continue to work with our team in the future. This case is a great example of how, through dedication to excellence and customer satisfaction, we can overcome any challenge with outstanding results.